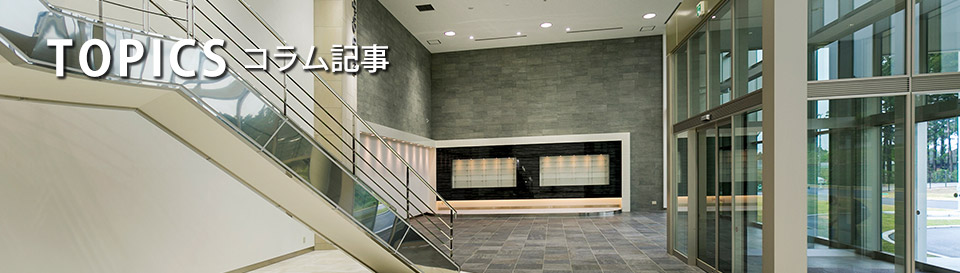
工場のレイアウトを最適化する!考え方・手順の概略まとめ
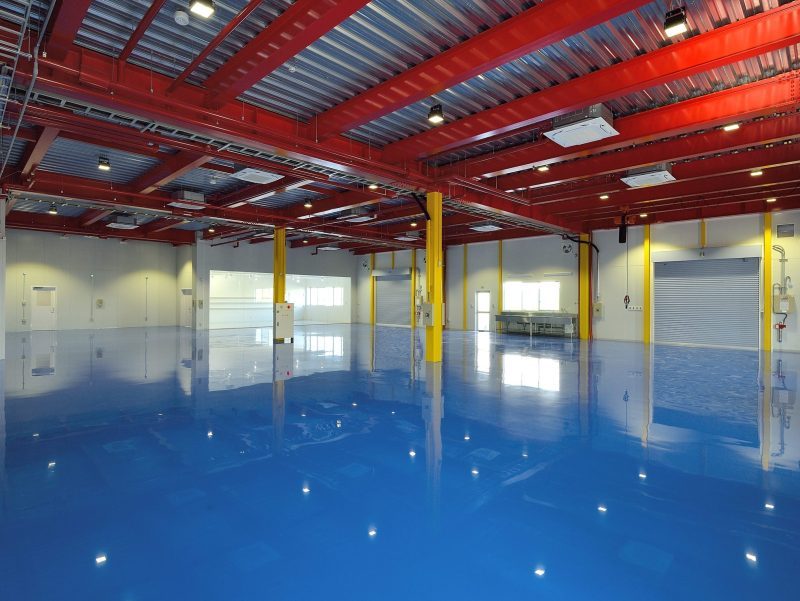
工場のレイアウトは、製品の品質から生産性にまでかかわり、ひいては人材確保にもかかわる重要な要素です。新しい工場を建設するときはもちろん、既存の工場のレイアウトも見直しをして改善すると後々プラスになります。ただし気軽にできることではないのもまた事実です。見直しする場合も十分に検討・検証することが必要です。
この記事では、レイアウトの種類や作成のポイント・手順など、工場のレイアウトの基本的な知識についてまとめます。改善・新規建築時の参考にしてください。
工場のレイアウトとは
工場のレイアウトとは、工場の建物や内部設備・施設の配置のことを言います。製品の品質・生産性や安全性・従業員満足度など色々な面にかかわり、工場建築においては重要な要素です。
レイアウトという観点から見た場合、工場は装置型工場・組立型工場に大別されます。
・装置型工場…大型の装置で製品を製造する工場(例:セメント・金属)
・組立工場…部品を組み立てて製品を製造する工場(例:家電・車)
装置型工場は大型の装置を配置するためレイアウトの変更が困難ですが、組立工場は変更が比較的容易という特徴があります。
レイアウトの種類
レイアウトの具体的な種類についてまとめます。設備の配置によって以下の4種類に分類することができます。
・ジョブショップ型
・ライン型
・セル型
・据え置き型
1つずつ詳細を見ていきましょう。
➀ジョブショップ型
「ジョブショップ型」は、機能別にまとめて設備を配置する方法です。
設備がまとまっているため、機能や単一作業の管理がしやすくなります。また小ロットに対応しやすいため、需要に合わせた調整がしやすいというメリットもあります。さらに人材育成の面でも、作業員が複数の設備を担当することが多く熟練作業者を育成しやすくなります。
ただし、作業ごとのリードタイムが異なり全体の把握が難しい、搬送経路が長く複雑になりやすいといったデメリットもあります。
ジョブショップ型の中でも、デジタル技術・ロボット化と組み合わせた「デジタルジョブショップ」が次世代の生産方式として期待されています。
②ライン型
「ライン型」は、工程の流れに沿って設備を配置する方法です。いわゆる流れ作業を行うためのレイアウトで、少品目大量生産に向いています。
大量生産に最適化したレイアウトのため、個々の製品の品質のブレが少なくなり製品の品質を安定させやすくなります。また工程を細分化し個々の工程が単純化されるため、自動化しやすいのもメリットの1つです。さらに作業者は細分化された工程を担当するため、作業者の担当する作業の種類が少なくなり習得期間が短くて済むのも特徴です。
デメリットとしては、需要の変化に対応しにくいこと、多品種の製造に向かないこと、単純作業になり作業者のモチベーション維持が難しいことが挙げられます。
自動車の生産現場などで広く採用されているレイアウトです。
③セル型
「セル型」は、作業者の周りに設備を配置して全工程が1か所で完結するレイアウトです。
一人の担当する工程が多くなりますが、その分作業者は完成までの作業を自分の責任で行います。達成感が得やすくモチベーションを維持しやすくなるほか、多品目の生産にも比較的対応しやすいというメリットもあります。
作業者が複数の設備を使って複数の工程を担当するという点では、ジョブショップ型に似ています。ジョブショップ型は設備の設置場所に作業者が移動していきますが、セル型は作業者中心に設備が配置されているため大きく移動する必要がありません。情報機器や家電の生産で導入されている方法です。
④据え置き型
「据え置き型」は、製品の周りを設備や人が囲むようにして製造するレイアウトです。設備や人中心のレイアウトではなく、製品を中心に考えたレイアウトです。
飛行機など、製品を動かすことが難しい大型の製品を作るのに用いられるレイアウトです。やや特殊なレイアウトだと言えるでしょう。
工場レイアウト最適化の考え方・ポイント
上記のようなレイアウトのうち自社に最適なものを選ぶ方法、工場のレイアウトを最適化するための考え方・ポイントをまとめます。具体的には4つのポイントがあります。
・動線
・作業効率
・保管場所
・エリア分け
これらのポイントを押さえることで、最適なレイアウトを実現することができます。1つずつ見ていきましょう。
ポイント➀動線
工程・設備間の動線が短くなるような設計が好ましいと言えます。動線は作業の能率に直結するためです。長い動線は時間のロスになり、移動中の事故などのリスクも高まります。
動線を短くするためには、レイアウトが作業の工程の流れに沿っていることが必要となります。また個々の動線が短かったとしても、交差や逆行があるとロスや事故の可能性が高まります。スムーズな流れが求められます。
さらに動線の広さ・幅が不十分だと、接触事故の原因となってしまいます。スムーズな流れを作るには、長さや流れの向きだけでなく広さも考慮に入れる必要があります。
さらに白線などで視覚的にも分かりやすくする必要もあります。十分な幅の通路を用意したとしても、保管場所代わりに使われてしまっては想定した機能が発揮されません。
ポイント②作業効率
作業効率を考えたレイアウトの設計も重要です。連続する工程はレイアウト上でも近くに配置することが必要となります。
作業効率を考慮してエリアのレイアウトに反映させることにより、時間の短縮やリスク減、連絡漏れの防止などにつながります。
エリア間の位置関係だけでなく、各工程内の道具や備品の効率的な配置もよく検討する必要があります。
ポイント③保管場所
保管場所の設計もレイアウトの最適化において求められます。床面(平面)だけでなく高さも利用した保管場所を作ると、スペースのムダを省いて有効活用することができます。
できるだけ動線の交差を避けるなど工程との関連も考慮に入れながら、何をどこに保管するか効率的に設計します。
また、進捗が違うものが混在しないように保管場所を分けることも重要です。判断に余計な時間がかかってしまうほか、製造上のミスが生まれるリスクも高まります。
ポイント④エリア分け
工場全体のレイアウトを最適化するためには、工場全体を俯瞰してエリアに分けることが非常に有効です。
たとえば、部外者が多く出入りする部門は出入り口の近くに配置します。さらに作業の効率とも深くかかわりますが、工程と工程の関連性によるエリア分けも重要です。騒音・振動などほかのエリアへの影響も考慮に入れましょう。たとえば大きな音の出る部署の隣に事務所があると、接客や電話応対に悪影響がありえます。
そのほか通用口や食堂、また厳密な衛生管理が必要な食品工場などではトイレの位置なども検討することが大切です。
レイアウト決定までの手順
次に、レイアウト決定までの手順をまとめます。工場のレイアウト決定の手法には、「SLP(システマティックレイアウトプランニング)」という方法があります。製品の量と種類、相互の関係性を考慮してトータルの搬送距離が最短になるよう設計します。上記のポイントで述べた動線や作業効率、エリア分けを具体化する考え方です。
SLPでは、次の4つのステップでレイアウト計画を行います。
1,物量の確認(P-Q分析)
2,動線の確認(物の流れ分析)
3,作業内容の確認(アクティビティ分析・アクティビティ相互関連ダイヤグラム)
4,スペースの確認(面積評価・スペース相互関連ダイヤグラム)
それぞれのステップについて見ていきましょう。
手順➀物量の確認(P-Q分析)
まず初めに、商品ごとの物量を確認します。製品(Product)ごとに生産量(Quantity)を確認し、多い順に並べます。基本的には、物量の多いものを優先的に考慮します。
物量の多いものは、製品別配置(ライン型)とします。大量生産に向くからです。少ないものは機能別配置(ジョブショップ型)とします。需要に合わせて臨機応変に対応することが可能だからです。中間のものはグループ別配置(セル型)とします。
手順②動線の確認(物の流れ分析)
次に、商品ごとに人・商品の動きを確認します。業務の流れを可視化するために、レイアウト上に流れを記入します。さらに動線に関して、距離・幅はどうか、交差・逆行がないかを確認します。
上でも述べた物量ともかかわりますが、使用頻度の高いエリアや物量の多い商品を重点的に確認しましょう。全体を最適化させるためには、頻度の高いところを優先することが効率的です。
手順③作業内容の確認(アクティビティ分析・アクティビティ相互関連ダイヤグラム)
次は関連する作業同士の場所を近くに配置するため、活動内容と相互の関連度を確認します。
まず、工場の構成要素「アクティビティ」(例:部門・機械・倉庫など)の種類や量を確認します。次にアクティビティ同士の関連の深さを確認します。「アクティビティ関連図表」を作成して可視化します。
アクティビティ関連図表の結果などをもとに、関連の深さを反映させて平面的に位置関係を示した図が「アクティビティ相互関連ダイヤグラム」です。必要なスペースはいったん保留とし、効率的な位置関係を設計します。
手順④スペースの確認(面積評価・スペース相互関連ダイヤグラム)
次にアクティビティごとに必要となるスペースを確認します。アクティビティ相互関連ダイヤグラムを踏まえて対象となるエリアの面積・形状・構造(梁の位置・床の耐荷重など)を反映した具体的な設計のベースを作成します。面積や形状が中心となりますが、構造面も検討漏れのないように注意しましょう。
アクティビティごとに必要な面積を算出し、アクティビティ相互関連ダイヤグラムにその面積を加味してスペース相互関連ダイヤグラムを作成します。これがほぼ理想のレイアウト・基本のレイアウトとなります。
手順⑤配列を検討
最後に、スペース相互関連ダイヤグラムに構造上の問題などないかを確認します。必要に応じてほかの案も作成し、多面的に比較検討のうえで最終的な決定を行います。ほかの案を作成するときも、面積・形状・構造を考慮します。
レイアウト案の検証方法
ツールを使ってレイアウト案を作成して比較・検証するときの具体的な方法をまとめます。主に次の3つのツールを使う方法があります。
・エクセルによるレイアウト図作成
・CADによるレイアウト図作成
・専用ソフトによるシミュレーション
それぞれに長所と短所があります。1つずつ具体的に見ていきましょう。
方法➀エクセルによるレイアウト図作成
エクセルでレイアウト図を作成することができます。「MicrosoftVisio」という作図専用のソフトもありますが、Visioなしでもエクセルでセルを方眼紙のように設定して作成することができます。
縮尺を計算してセルのサイズを設定します。それをもとに形状と大きさを縮小・再現した床面の図を作って作図のベースとし、その上にオブジェクトを設備に見立てて配置します。オブジェクトも縮尺に合わせた数値を入力して、図の上で大きさを反映させます。
作成できるのが平面図に限られ、高さを加えた立体的な検討ができないというデメリットがあります。しかし普遍的なソフトを使用するため、手軽に作成・検証することができます。
方法②CADによるレイアウト図作成
CADによりレイアウト図を作成することもできます。
これまでは広く汎用2D CADを使用してレイアウト図が作例されてきました。エクセル同様手軽というメリットがありますが、やはり高さが分からないためレイアウト変更後に不備が発見されることがあるというデメリットがありました。
そのデメリットを解決するため、最近は3D CADを使うことが増えています。3D CADでは、より詳細な検証が可能です。
方法③専用ソフトによるシミュレーション
レイアウト専用のソフトを使ってシミュレーションする方法もあります。立体的な空間の中で実寸でのレイアウト検証が可能です。詳細なレイアウトの作成と比較検討ができます。
さらにツールにもよりますが、レイアウトの配置のみならずそのレイアウトで工場を稼働させた場合のシミュレーションをすることができます。対応ツールであれば、条件を考慮してデータを算出し、生産能力などを検証することが可能です。事前に詳細な比較検討をすることができ、最適なレイアウトの決定に役立ちます。
CADのデータを読み込めるソフトが多くあり、既存のデータがある場合はデータを流用することが可能です。機能が充実しているというメリットがありますが、当然その分コストがかかります。
工場レイアウトでお困りならファクトリアへご相談を
工場のレイアウトでお困りでしたら、ぜひ私ども「ファクトリア」にご相談ください。ファクトリアは快適な作業環境を実現し、企業価値を高める工場を目指す「工場建設のトータルサービスブランド」です。
工場建築の実績も多数あり、食品から工業製品までさまざまな製品の工場建築の経験があります。条件をご提示いただければ、蓄積したノウハウから御社に最適なご提案が可能です。設備や機能面はもちろん、モチベーションの上がる内装や外観にこだわったデザインも得意です。もちろんレイアウト以外の面でのご相談も承っております。
ご興味おありの場合・ご質問のある場合はお気軽にお問い合わせください。
-
工場の改修・改善工場の外壁塗装の「色」選びのポイントとは?定番色ごとの特徴も紹介
工場の外壁塗装は見た目を整えるだけでなく、機能性や安全性、企業イメージの向上にもつながる重要な要素…
-
工場の改修・改善食品工場の自動化のポイントやロボットの導入メリットをご紹介
工場では生産性の向上や効率化、そして人手不足の問題を解決するために、ロボットの導入など自動化の動き…
-
工場の改修・改善工場・倉庫の寒さ対策総まとめ!暖房器具や断熱対策で作業効率向上へ
冬場の工場や倉庫は寒さが厳しく労働環境が過酷になるため、多くの工場管理者・従業員が防寒対策の難しさ…
-
工場の改修・改善工場の天井や屋根の断熱・遮熱で得られるメリットと具体的な施工方法
工場や倉庫において夏の暑さや冬の寒さ対策は大きな課題となっています。工場や倉庫はその構造上、家屋な…