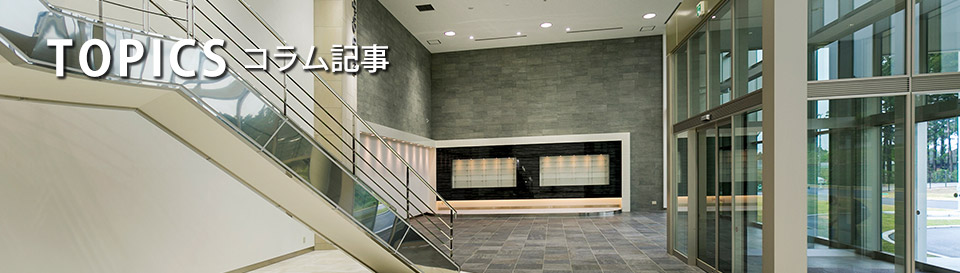
工場の省人化は重要課題!メリットや省人化を実現する4つの方法とは?
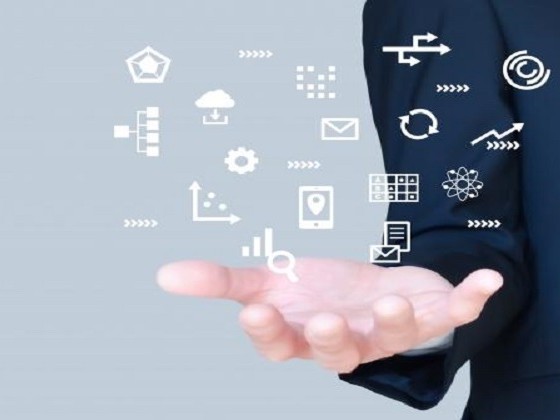
近年、工場における人手不足の深刻化や人件費の高騰、作業の効率化が求められる中、省人化は避けて通れない課題となっています。この状況を打破し、生産性を維持・向上させるための重要な戦略が、工場の「省人化」です。
省人化を進めることで、コスト削減や生産性向上が期待できるだけでなく、働く従業員の負担軽減にも繋がります。とはいえ、省人化を実現するためには、それに見合った技術や運用の変革が必要です。
本記事では、工場における省人化のメリットや、実現するための具体的な方法について詳しく解説します。これを機に省人化を検討し、より効率的で持続可能な工場運営を目指してください。
省人化とは?
省人化とは、可能な限り少ない人員で作業を行う取り組みのことです。業務の見直しや無駄の削減を通じて作業の効率化と自動化を図るとともに、人的リソースを確保し、経済的で持続可能な生産を目指す重要な戦略です。
主に設備や作業プロセスの改善、作業の振り分け、機械やロボットの導入などが具体的な手法として挙げられます。
「省力化」との違い
省力化とは、作業員の業務負担を軽減するための取り組みを指します。具体的には、作業の無駄を削減し、機械の導入で効率化を促進することが主な手法です。
しかし、人員の削減を直接目的としません。例えば、作業の90%を自動化した場合、残り10%の作業は依然として人間が行う必要があります。
つまり、省力化は業務効率を向上させても人員削減には繋がらないことが多いのに対し、省人化は人員削減を重視しているという点で異なります。
「少人化」との違い
少人化とは、省人化をさらに進めた概念で、生産量の変動に応じて最適な人数で業務を運営することを目指すものです。
例えば、生産需要が高まれば必要な人員を増やし、需要が減少すれば人員を減らすといった動的な配置が求められます。これにより、変動する市場ニーズに対応しつつ、最小限の人的コストで効率的な生産が可能となります。省人化が基礎的な人員削減を図るのに対し、少人化は需要に応じた柔軟な人員管理を行う点で違いがあります。
工場において省人化が求められる理由や取り組むメリット
ここでは、工場で省人化が急務となっている理由や、省人化に取り組むメリットについてご紹介していきます。
人手不足の解消
省人化は、人手不足の課題解決に大きな役割を果たします。少子高齢化が進む日本では労働力人口が減少しており、特に製造業では優れた技術者の不足が顕著です。
そこで省人化によって機械やシステムを導入することで、非熟練者を支援しつつ、優秀な技術者の負担を軽減することができます。この取り組みは従業員の定着率を上げ、離職率の低下にも貢献します。
生産性の向上
省人化の導入により、製造工程全体の生産性が向上することもメリットのひとつです。新しい設備やシステムを導入することで、無駄な作業を削減し、業務プロセスを効率化できます。
この結果、人的リソースの負担が軽減され、より少ない労力で高い生産性を実現できます。さらに、デジタル技術やAIを活用することで業務の改善が進みます。生産体制の最適化は、中長期的な増産計画も可能にし、企業の競争力を維持するための重要な要素となります。
働き方改革の推進
省人化は働き方改革を推進する力強い手段です。自動化や効率化を進めることにより、従業員にかかる作業負荷が軽減され、安全で快適な作業環境が整います。
これにより、時間外労働の削減が促進され、有給休暇や育児休暇の取得がしやすくなります。また、長時間労働の是正や作業環境の改善が進むことで、従業員はより柔軟で働きやすい職場環境を手に入れることでき、ワークライフバランスの向上にもつながるでしょう。
人件費の削減
省人化により、同一の生産活動をより少ない人手で行えるようになるため、人件費の削減が期待できます。人件費の抑制が進むということは、製品のコスト競争力が向上し、企業全体の収益性が強化されることにもつながるでしょう。
また、余剰となった資金を新たな設備や技術への投資に回すことも可能となり、さらなる生産性向上を実現できます。
品質の均一化
省人化を通じて自動化技術を導入することにより、品質の均一化も実現します。人の手作業に依存する場合、技術者ごとの技術差によって製品の品質がばらつくことがありますが、機械化することで一定の品質を保つことが可能です。
これにより品質管理が容易で、企業の信用も向上するでしょう。また、技術の標準化と可視化を図ることにより、熟練者に依存せずに製品の品質を維持できるため、技術継承もより簡単になります。
作業環境の改善
省人化は作業環境の向上にもつながります。人手不足が深刻化すると、従業員一人あたりにかかる業務負担が増加し、ストレスや労働災害のリスクが高まります。
しかし、省人化を進めることで業務が効率化され、負担が軽減。従業員のモチベーションが向上します。
また、機械やロボットの導入により危険な作業が削減され、安心安全で快適な作業環境が整うでしょう。
技術・技能承継問題の解消
前項で少し触れましたが、省人化は、技術や技能の承継問題を解消する手段としても有効です。熟練工の退職に伴い、高度な技術や技能の継承が難しくなる状況において、機械化や自動化を導入することで、技術の標準化が進みます。
これにより、特定の人材に依存せず、技術の再現性が向上します。さらに、技術をデータ化・可視化することで知識の共有が促進され、技術や技能の継続的な継承が可能となるのです。
工場の省人化のデメリットや注意点
工場の省人化には、先に挙げた多くのメリットが存在しますが、その一方でデメリットや注意点もあります。
これらは、機械の導入時における初期コストや維持費、設定や調整にかかる時間、作業スペースの不足、さらにはDX人材の確保や育成に関する問題などです。
適切な対策を講じなければ、省人化の進行が企業活動にとって逆効果になる可能性もあります。まずは以下のデメリットや注意点について詳しく見ていきましょう。
機械の導入やメンテナンスにコストがかかる
省人化を進めるための機械の導入には当然コストがかかります。新たな機器を購入するための初期費用はもちろん、日々のメンテナンス費用も無視できません。
さらに、機械を効果的に活用するためには、従業員の教育も欠かせません。これには教育コストがかかり、研修資料の作成やトレーニングによる業務の一時的な停滞も考えられるため、導入時の計画には慎重さが求められます。
自動化などの設定・調整時間が必要
製造過程における自動化は、生産効率を大きく向上させる可能性がありますが、設定や調整には時間がかかります。自動化システムに変更を加えるたびに、詳細な設定が必要で、生産ラインを一時的に停止することも避けられません。
また、工程の一部を自動化すると、手作業との連携が複雑化することもあり、作業全体の流れをスムーズにするための工夫が求められます。
作業スペースの確保も必須
機械やロボットを導入する際には、それらを置くためのスペースを確保する必要があります。特に工場内のスペースが限られている場合、既存の作業スペースが圧迫される可能性があるでしょう。
これにより、従業員の作業効率や安全性が損なわれることも考えられるため、慎重な位置決めと環境設計が必要です。省人化を進めつつも、従業員が安全かつ快適に作業できる環境づくりを心掛けましょう。
DX人材の獲得・育成も不可欠
省人化を積極的に進めるためには、DXやITに詳しい人材の獲得と育成が不可欠です。しかし、現実にはこのような人材は不足しており、育成には時間とコストがかかります。
採用が難しい場合には、外部の専門家を活用するなどの柔軟な対策が効果的です。企業の競争力をさらに高めるためには、新たな技術を活用できる人材の育成に注力し、長期的な人材戦略を考えることが求められます。
工場における省人化の流れ(進め方)
ここでは、省人化を実現するための具体的な進め方について、各ステップでの詳細な手法を解説します。
①既存業務の分析・見直し
省人化を実現するためにはまず、現在の業務がどのようになっているかを把握することが重要です。無駄な業務や非効率なプロセスはないか、また作業負担が大きすぎる工程はないかなど、詳細に分析を行います。
既存の生産プロセスを洗い出し、工程を細分化して無駄をチェックすることで、どの部分で改善が必要かを明確にします。こうした作業は、のちの自動化の候補を決定する際に大いに役立ちます。
②作業の標準化・マニュアル化
既存の業務分析が完了したら、次に作業の標準化に焦点を移します。作業手順や方法にばらつきがあると、作業効率が低下しやすくなります。
そこで、効率的な作業手順を作業員全員が共通して理解できるようにマニュアル化することが大切。マニュアル化することで、誰でも同じレベルの効率性で作業がこなせるようになり、業務の属人化も防ぐことができます。
③現場への周知・従業員への教育
標準化された作業手順を従業員に浸透させるためには、しっかりとした教育が不可欠です。新しい手順がなぜ必要なのか、どのような効果が見込まれるのかを明確に説明し、従業員とのコミュニケーションを図りましょう。
作業の標準化を進める際には、従業員のスキル向上も必要であり、特にITスキルや新しい技術への対応力を養うための継続的な教育が必要です。
④最新技術や設備導入による自動化
工場の省人化を進める最後のステップとして、最新技術や設備の導入による自動化があります。ロボットやAI、IoTを活用することで、これまで人が行っていた作業を機械が代行し、大幅な効率化と生産性向上を図れます。
特に自動化が進んでいない工程などの領域を見直すことで、労働力の削減と同時に品質の向上を実現できるでしょう。
工場の省人化を実現する具体的な4つの方法
最後に、工場の省人化を実現する具体的な方法をご紹介します。
次に紹介する手法を効果的に組み合わせることで、人員不足の解消や業務の効率化、生産性の向上を図ることが可能です。それぞれの方法についてみていきましょう。
業務の見直し・不要な工程の改善
業務の見直しと不要な工程の改善は、工場の省人化において基本的かつ重要なステップです。特に古くからの生産体制が続いている工場では、時代に合わなくなっている工程や、今はもう必要のない作業が慣習的に残っている場合があります。
これらを洗い出し、作業プロセス全体を見直すことで不要な部分を削減し、業務効率を高めることができます。この改善プロセスは、社員全員の意識改革を促し、全体的な生産性の向上にもつながるでしょう。
産業用ロボットの導入
産業用ロボットの導入は、省人化の最も代表的な方法のひとつです。工場で従来人が行っていた溶接、ハンドリング、組み立てなどの作業を自動化されたロボットへ移行することが可能です。
ロボットは24時間稼働が可能で、品質の向上や不良率の低減に効果を発揮します。また、特定の工程を省略できるため、人件費の削減や作業者の負担軽減にもなります。このように、適切なロボットの導入は、工場の運営を大きく変革します。
関連記事:食品工場の自動化のポイントやロボットの導入メリットをご紹介
AIやIoTによる業務のデジタル化
AIやIoTは、工場の業務デジタル化を進めるための強力なツールです。AIを活用した製品の品質検査や、不良品の発生率低下に加え、IoTを利用した設備データの可視化が可能です。
これにより生産ラインの状況を一目で把握でき、リアルタイムな管理が実現します。さらに、デジタル化された情報は蓄積され、後の分析や新製品開発の基盤となるのです。
クラウドカメラやAIカメラの導入
クラウドカメラやAIカメラの導入は、遠隔地からの生産工程監視を可能にし、省人化に役立ちます。これらのカメラは、リアルタイムで製造状況を確認できる機能を持っており、異常検知時には即座に通知を行います。
この機能により、常時現場にいなくても迅速な問題対応が可能となり、作業員の労力を他の業務に集中させることができます。
今ある課題を把握し、工場の省人化を実現しましょう
将来的な人材不足やコスト増加が懸念される中で、省人化はますます重要な課題となります。本記事を参考に現状の課題を正確に把握し、適切な対策を講じることが、工場の持続可能な発展に繋がります。
しかし、設備の選定やレイアウトの最適化など、専門的な知識が必要な場面も多く、適切なパートナー選びが成功の鍵となります。
そこで、ぜひ私ども工場建設のトータルブランドサービス【ファクトリア】にご相談ください。ファクトリアは工場建設に関するあらゆるニーズに対応する専門家集団です。
お客様の課題やご要望を丁寧にヒアリングし、工場建設から省人化まで、ワンストップでサポートいたします。省人化を実現し、持続可能な工場運営を目指すなら、ぜひファクトリアにご相談ください。
-
工場運営食品工場に潜む事故リスクや労働災害の事例 | 工場老朽化の危険や対策も紹介
食品工場は人の食生活を支える重要な施設ですが、その裏では様々な事故リスクや労働災害の危険が潜んでい…
-
工場運営工場の省人化は重要課題!メリットや省人化を実現する4つの方法とは?
近年、工場における人手不足の深刻化や人件費の高騰、作業の効率化が求められる中、省人化は避けて通れな…
-
工場運営工場の電気代削減策11選 | 具体的な削減・節電方法やポイントを紹介
電気代の高騰は、企業の経営を直撃する深刻な問題です。特に、多くの電力を消費する工場において電気代の…
-
工場運営【施工事例あり】食品工場のゾーニングとは?目的や重要性、ポイントも解説
食の安全に対する意識が高まる中、食品工場の衛生管理はますます厳しくなってきています。そのような中で…