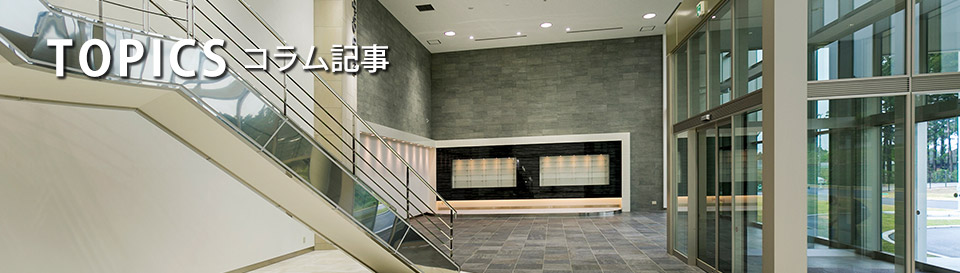
製造業で工場の生産性を向上させるには?自社で使える問題の原因発見と向上の方法
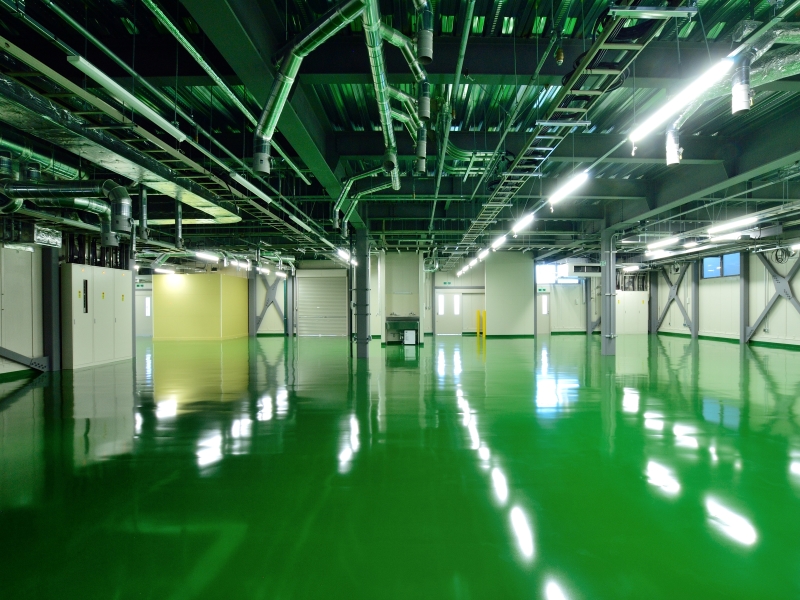
国際的に見て日本の生産性が低いと言われています。社会が大きく変化する現在、国内企業の生産性向上が急務となっています。もちろん製造業も同様です。
この記事では、工場の生産性を向上させるために問題点を発見する方法と問題を改善して生産性を向上させる方法についてまとめます。活用できる助成金についても紹介するので、企業のご担当の方はぜひ参考にしてみてください。
工場における生産性とは
「生産性」とは、ヒト・カネ・モノなど経営資源を投入(インプット)して、どれだけの成果(アウトプット)があったかという割合を示すものです。「アウトプット÷インプット」で表すことができます。少ない資源で大きな成果が得られるほど生産性が高いことになります。
つまり生産性を上げるためには、同量の資源でより大きな成果を得るか、より少ない資源で同じ成果を得るかのどちらかを目指すことになります。
投入する経営資源や得られる成果の種類によって、生産性は何種類かに分けられます。この記事では、投入した労働力に対してどれだけの付加価値を生んだかという「付加価値労働生産性」を扱います。製造業をはじめビジネスで「生産性」と言うときは、この付加価値労働生産性を指すことが多いからです。この「付加価値」は、「粗利」に近いイメージです。
なぜ生産性向上が必要か
「なぜ生産性向上が必要か」という理由はいくつかありますが、一言で言えば企業・国の競争力に大きく関わるからです。
そもそも諸外国と比べたとき、OECD加盟37カ国中21位と日本の生産性は低いのが現状です。アメリカの約6割、生産性の高いアイルランドの半分以下の生産性です。さらに今後労働人口減が確実となっている中、国際的な競争力のためにも生産性向上は急務です。
さらに生産性は「働き方改革」にもかかわるなど、ワークライフバランスにも影響します。このようにあらゆる意味で生産性向上が必要だと言えます。
生産性向上のメリット
生産性が向上することには、さまざまなメリットがあります。もちろん競争力が高まるということになるのですが、もう少し具体的にメリットについて解説します。
まず生産性が向上すると生産量が増えて販売量が増えます。その結果売上が上がり、利益も増やすことができます。さらに同じ量の製品を生産するのにもコストが下がって、利益率が改善します。そういった意味でも利益が増えます。
そのほか生産性が上がると、同じ量の製品をそれまでより短い時間で生産できるようになります。その結果労働時間が短縮され、労働条件が改善するため働き方改革につながります。さらに生産性向上のために作業の標準化が進むと、品質の安定につながります。安定した品質の製品は売れやすくなるので売上が上がります。
工場の生産性を下げる原因「ムリ・ムダ・ムラ」
生産性を下げる原因を取り除けば生産性は向上します。生産性を下げる原因についてはいろいろな説明がありますが、まとめると「ムリ・ムダ・ムラ」が原因と言えます。ケースバイケースとなる原因の具体例を知ることも参考になりますが、自社にムリ・ムダ・ムラがないか考える方が自社特有の原因発見と改善につながります。
以下、ムリ・ムダ・ムラについて具体的に解説していきます。
ムリ:目的>手段
「ムリ」は、手段より目的の方が大きくなっている状態です。言い換えると、人や設備の能力を超える作業を行うことです。工場で言えば、人手不足の状態や設備の性能以上に製品を製造している状態を指します。作業者に負担のかかる環境もムリに当たります。たとえば高温や過度な重量物を扱わなければならない状態などです。
ムリのある状態では、人や設備に過度な負担がかかることになってしまいます。ムリは人の疲労やケガ・モチベーション低下、設備の故障や不良品などの原因です。その結果、生産性の低下を引き起こします。
ムダ:目的<手段
「ムダ」は目的よりも手段の方が大きくなっている状態です。人や設備を活用しきれていないことだと言えます。工場で言えば、人や設備の能力より製造量が少なく、稼働していない状態が生まれていることを指します。あるいは不要な作業をしていたり、不要な在庫があったりする状態です。
トヨタの生産方式では、次の「7つのムダ」があるとしています。
・加工のムダ:不要な工程
・在庫のムダ:材料・製品などの過剰在庫
・不良や手直しのムダ:不良品の廃棄・手直し
・作りすぎのムダ:製品の作りすぎ
・手待ちのムダ:人・設備が稼働していない状態
・動作のムダ:作業中の不要な動き
・運搬のムダ:材料・製品の必要以上の運搬
ムダがあると経営資源を活用しきれていない状態にあり、ポテンシャルより生産性が低くなってしまいます。
ムラ:ムリとムダの混在
ムラは、ムリとムダが混在している状態です。手段と目的のバランスが入れ替わったりして、ムリになったりムダが生じたりすることを言います。
工場で言えば、時期や作業者によって生産量・作業量・作業手順・在庫・製品品質などにバラつきがあることです。そのほか作業の連携がうまく行かず、待ちが生じている場合もムラに当たります。作業にかかる時間が作業者間で釣り合っていない状態・バラつきがある状態だからです。
あらゆる点で標準化してバラつきをなくすこと、バラつきのない状態を維持することが生産性向上のカギとなります。
生産性向上は階層別に取り組む
生産性の低下や停滞にはさまざまな要因があります。工場でムリ・ムダ・ムラを発見しても、原因をたどると現場の工夫だけではどうにもならないこともあります。たとえば社員教育の不足・評価制度の不備・設備の老朽化などです。
製造業で生産性向上を目指す場合は、問題の原因については工場だけでなく管理部門などあらゆる面を分析すべきだと言うことができます。そのうえで工場で改善できることから改善していきましょう。
工場でできる生産性向上の手順
工場でできる生産性向上の手順についてまとめます。次の手順で行います。
1、問題点を発見する
2、解決策を考える
3、解決策を実行する
4、マニュアル化・仕組み化する
それぞれの手順について見ていきましょう。
手順➀問題点を発見する
原因が会社の制度にあるにしても、問題は現場で形になります。まずは現場の観察を通じて問題点を発見することが大切です。
実際に作業している社員にヒアリングを行いましょう。日々の作業から問題点に気付いている場合もあります。ただし自分のムリ・ムダ・ムラに自覚がない場合もあるので注意が必要です。そのほかの方法としては、業務のプロセスを可視化すること、作業を録画して分析することなどが挙げられます。
詳しくは後述しますが、問題点は動作・工程・設備などに分けることができます。
手順②解決策を考える
問題点が明らかになったら、それを解決する方法を考えます。ムダな動作をなくすほか、工程間の最適化、レイアウトの変更や5Sによる環境整備などを行います。具体例は後述します。なお目先のことしか考えない効率化は製品の品質を下げる原因です。製品の品質を落とさないという視点は忘れてはいけません。
作業者によって作業効率に差がある場合は、効率の高い人と低い人の作業を比較しましょう。効率の高い人の作業を参考にするとムダの発見につながります。
動作などは現場で改善できますが、そうでない場合もありえます。たとえば成果を出しても評価されず、モチベーション低下の原因になっているなどといったケースです。それは現場でなく評価制度の問題です。現場でできること、経営陣の協力が必要なことなど分けて考えます。
またコストが必要となる解決策は費用対効果も考慮しましょう。コストがかかる場合は、一度変更すると簡単には変えられないからです。
手順③解決策を実行する
次に実際に改善策を実行してみて、効果測定を行います。PDCAを回しながら、よりよい方法にブラッシュアップします。場合によっては別の方法を試してみます。試行錯誤しながら最適な方法を探り当てましょう。
解決策は誰もが同じように生産性の高い作業ができるようなものでなくてはなりません。属人的になってしまうと、ムラの原因になるからです。標準化することを前提にしましょう。
手順④マニュアル化・仕組み化する
改善が実現できたら、その方法を標準化します。動作はマニュアル化、工程は仕組み化します。
皆が同じように作業できるようにならないと、ムラの原因となってしまいます。結局生産性は向上しないことになってしまいます。意図や背景など含めて考えや手順などの統一を徹底しましょう。
生産性向上策の例
次に、生産性を向上させる施策の例を紹介します。以下の例が挙げられます。
・動作の改善
・工程の改善
・レイアウトの改善
・IT化・新設備の導入
それぞれについて、さらに具体的な例を交えながら解説します。
向上策の例|動作の改善
動作に問題がある場合の改善例としては、ムダな動きの排除があります。ムダな動きの例としては、持ち替える、しゃがむ、調べるなどがあります。品質を保ちつつ、より少ない動作で作業を行う方法を考えましょう。ムリな動きを改善させる場合もあります。たとえば不自然な姿勢をしなくて済むようにします。
動作の問題を解決するためには、作業環境の改善が必要な場合もあります。たとえば台の高さを変えたり、作業手順に合わせたレイアウトに変更したりします。改善した作業を定着させるためには、作業手順の再教育とマニュアルの整備が必要です。
向上策の例|工程の改善
工程に問題がある場合の改善策では、作業の流れを滞らせている原因を排除します。
ムダな工程を排除することで工程が改善される場合があります。ムダな工程の例としては、積み替えや仮置きなどがあります。ムリな工程を改善する方法もあります。たとえば、人材配置を改善して重量物を扱う部署に人を増やす、在庫確認や製造量決定の方法を見直すなどが挙げられます。
環境を改善することで工程も改善する場合もあります。
向上策の例|レイアウトの改善
レイアウトに問題がある場合、その問題点を改善すると動作や工程が改善されることにつながるケースが多くあります。作業手順や工程の流れ・作業動線に合わせたレイアウトを検討しましょう。
具体的には、「5S」による環境整備が挙げられます。5Sとは「整理」「整頓」「清掃」「清潔」「しつけ」のことです。
工具を並べる場所を変える程度ならすぐにできますが、機械の配置を変える場合は大規模になることもあります。変更にも手間がかかりますし、元に戻さなければならなくなった場合も労力が必要です。よく検討してからにしましょう。
向上策の例|IT化・新設備の導入
新しい設備やシステムを導入することで生産性が向上する場合もあります。たとえば生産管理システムを導入すれば、在庫管理を改善して在庫のムダ・作りすぎのムダを解消することが可能です。新しい製造設備を導入すれば、生産能力アップにつながってムリを解消することができます。
このように新しいシステムや設備の導入は、ムダな工程の解消、ミス発生の排除と不良や手直しのムダの解消に役立ちます。将来性を見据えたDX導入という点からも、新しいシステムを導入したいところです。
生産性向上に活用できる助成金
生産性向上のために活用できる助成金があります。ここでは3つの助成金について紹介します。
●業務改善助成金
中小企業・小規模事業者が生産性を向上させるための取り組みを支援するものです。従業員の昇給が条件となっており、最大600万円が助成されます。機械設備やコンサルティングのほか、人材育成・教育訓練も助成対象です。
●IT導入補助金
中小企業がITツールを導入する経費の一部を補助し、業務効率化・売上アップをサポートします。3種ある枠によりますが、最大450万円補助されます。ソフトウェア購入費・クラウド利用料・導入関連費のほか、枠によりハードウェア購入費が対象となります。
●ものづくり補助金
中小企業が経営革新のために設備投資するときなどに使える補助金です。条件により、最大5,000万円まで補助されます。機械装置・システム構築費ほか対象は多岐に渡っています。
それぞれ助成・補助を受けるための条件や、金額を決める条件があります。自社の取り組みに合わせて活用できそうな制度があれば、より詳しく調べてみてください。
生産性を向上できる工場建設ならファクトリアへ
工場のレイアウトは生産性に大きく影響します。生産性の高い工場建築を考えているなら、私ども【ファクトリア】にぜひご相談ください。
ファクトリアは快適な作業環境を実現し、企業価値を高める工場を目指す「工場建設のトータルサービスブランド」です。
工場建設を多数手がけており、作業効率にプラスとなる動線設計など得意としています。動線設計は食品工場のISO対応などにも役立ちます。新築は制限が少ない中でのご提案が可能で、より生産性を高めるアイディアを実現できます。品質はもちろんですが、コスト面でも追加費用の発生を抑えています。
ご興味おありの場合・ご質問のある場合は、お気軽にお問い合わせください。
-
工場の改修・改善工場のレイアウトを最適化する!考え方・手順の概略まとめ
工場のレイアウトは、製品の品質から生産性にまでかかわり、ひいては人材確保にもかかわる重要な要素です…
-
工場の改修・改善工場の外壁塗装の「色」選びのポイントとは?定番色ごとの特徴も紹介
工場の外壁塗装は見た目を整えるだけでなく、機能性や安全性、企業イメージの向上にもつながる重要な要素…
-
工場の改修・改善食品工場の自動化のポイントやロボットの導入メリットをご紹介
工場では生産性の向上や効率化、そして人手不足の問題を解決するために、ロボットの導入など自動化の動き…
-
工場の改修・改善工場・倉庫の寒さ対策総まとめ!暖房器具や断熱対策で作業効率向上へ
冬場の工場や倉庫は寒さが厳しく労働環境が過酷になるため、多くの工場管理者・従業員が防寒対策の難しさ…