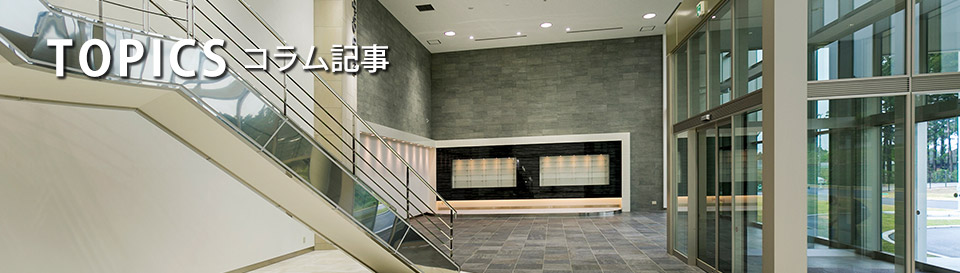
工場でのヒヤリハット事例まとめ【原因・対策・報告も解説】
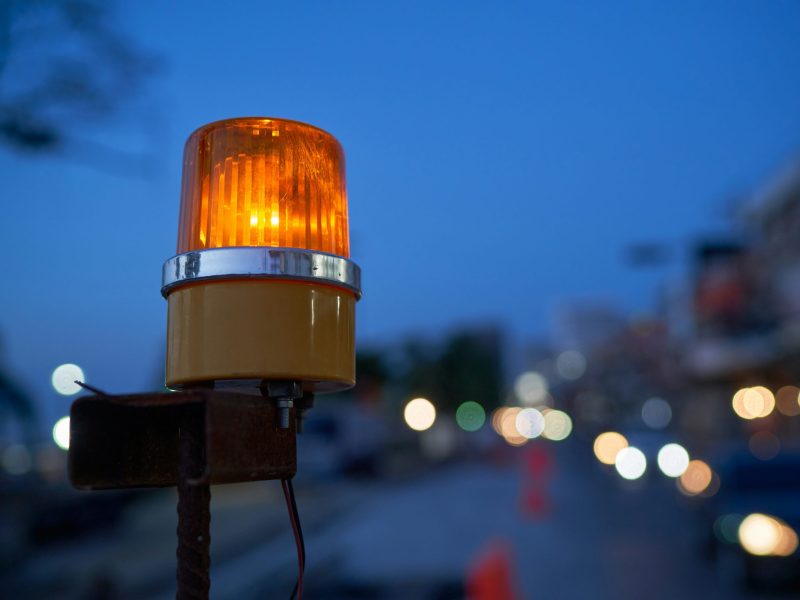
工場で働いていると一度や二度は「ヒヤリハット」の経験があるのではないでしょうか。ヒヤリハットを放置しておくと重大な事故が起こるリスクが高まります。逆にヒヤリハットの予防は重大な事故の予防につながります。貴重な人材のケガなどを避けられるほか、労災を使わずに済むことが可能です。
この記事では、工場のヒヤリハットの事例の紹介と、その原因・対策・報告について解説します。ご担当者様はぜひご一読ください。
そもそもヒヤリハットとは
厚生労働省によれば、「ヒヤリハットとは、危ないことが起こったが、幸い災害には至らなかった事象のこと」と定義されています。危険を感じて「ヒヤッとした」「ハッとした」もののそれだけで済んで大事に至らなかったこと、重大な事故や災害の一歩手前の出来事だと言えるでしょう。
しかし冒頭で述べたように、事故に至らなかったからといって何も対処しない場合、大きな事故のリスクが高まります。対処のためにはヒヤリハットがどのような内容だったかを把握する必要があります。
工場でのヒヤリハットの事例
次に、工場でのヒヤリハットの事例について紹介します。厚生労働省のサイト「職場の安全サイト」から、製造業・加工業など工場での事例を場面別にまとめます。具体的には以下の場面です。
・台車の使用時
・フォークリフトの作業時・移動時
・製造機器・工具の使用時
・清掃・修理時
・重量物などの運搬時・作業時
1つずつ見ていきましょう。
事例 | 台車の使用時
台車の使用時の事例は運搬中のほかにもいろいろなパターンがあります。つまり運搬以外でも注意が必要です。次のような事例があります。
・台車で運搬中作業員と衝突し転倒した
・女性作業員が台車上の容器の移動作業中、容器を持ち上げたときに足を台車上に乗せてしまい、台車が動いて転倒しそうになった
・床面とエレベーターの「かご」の間の段差に引っ掛かり、引き出そうとしていた台車が転倒した
1つめの衝突・転倒の事例は、死角だったことや滑りやすい床面で台車のブレーキが効きにくかったことなど複合的な要因もあります。
事例 | フォークリフトの作業時・移動時
フォークリフトのヒヤリハット事例からは、移動中・作業中の対人の危険性、作業中の荷物への危険性などが読み取れます。備品の保管状態など環境が原因となっているケースもあります。
・フォークリフトと通行者が衝突しそうになる
・作業場を歩いていたところ、フォークリフトが方向転換のためバックしてきて激突しそうになった
・破損パレットにフォークが当たり倒壊しそうになった
・フォークリフトがボンベに衝突し、アセチレンが漏洩した
3つめの破損パレット事例は、フォーク差し込み箇所が破損して差し入れ不能になっていたパレットをフォークの爪で押してしまったものです。最後のボンベの例は、通路横に立てかけておいた不安定なボンベが倒れたところをたまたまフォークが通ったという事故です。
事例 | 製造機器・工具の使用時
製造機器や工具を使用しているときのヒヤリハットの事例は、製造業では非常に多くあります。巻き込まれ・挟まれ・突発的な動きによるケガなどの危険性が示唆されます。機器への巻き込まれや挟まれは衣服などが原因の場合もあります。
巻き込まれ・挟まれのヒヤリハットの事例で使われていた機器は、横中ぐり盤・ローラー・箱詰機などです。またボール盤や樹脂混錬機の作業中、手袋をしていたせいで巻き込まれそうになった事例があります。防寒頭巾の裾がローラーに巻き込まれそうになった事例もあります。
突発的な危険な動きの例を挙げます。
・フラッシュ材の切断中、材料が飛び出して人にあたりそうになった
・粉砕機から外れた高圧空気ホースが危うく顔に当たりそうになった
工具のヒヤリハットとしては次の事例がありました。
・電動丸ノコを使用して作業中、回転中に歯に手が触れそうになった
・グラインダーで鋼板の面取りを行おうとしたところ、鋼板が足元へ落下した
そのほか機器や工具そのものではなく、ボール盤で発生する「キリ粉」が眼に入りそうになるという事例もあります。
事例 | 清掃・修理時
製造の作業中だけでなく、清掃や修理中の事例も多数あります。機械の動作中や電源が入ったままで作業することは危険です。電源を切っていても、たまたま電源に触れて通電させそうになった例もあります。
・帯鋸盤を動かしたまま盤上の清掃をしようとして、帯鋸盤に手が近づき、回転している刃に手が当たりそうになった
・製麺機の清掃中、カット箇所に指が挟まれそうになった
・主電源スイッチを切った上での配電盤の配線変え作業
1つめ・2つめの事例は、それぞれ帯鋸盤・ローラーを動かしたままだったことが原因です。3つめの例は、主電源のスイッチは切っていたものの腕が振れてスイッチを入れてしまいそうになった事例です。ほかにも、作業許可なしで作業に着手したうえ、手順が不適切だったことが原因の例もあります。
さらに休憩中の事例もあります。
・暖房用のジェットヒーターで暖を取っていて火傷しそうになった
・喫煙所で吸殻が発火した
あらゆる場面で注意が必要です。
事例 | 重量物などの運搬時・作業時
重量物などの運搬や作業における事例もあります。以下はクレーンなどを使用中の事例です。
・積み荷の揺り返しによりフレコンバッグが当たり、荷台から転落しそうになった
・鋼材の吊上げ作業において、吊上げた鋼材のバランスが悪く、マグネットから外れて落ちそうになった
・鉄板がシャックルから外れた
・フレコンバッグの繊維ベルトが切断した
上の3つは操作やバランスなど人的理由によるもの、4つめは備品の状態によるものだと言えます。
ほかにも、人力での運搬中の事例もあります。
・アルミパネルを運ぶ際、パネルを落とし足に当たりそうになった
重量物を扱っている最中の事故は被害が大きくなる可能性があるので、あらかじめ芽を摘んでおく必要があります。
ヒヤリハットとハインリッヒの法則
ヒヤリハットの対策について考えるとき、「ハインリッヒの法則」が参考になります。ハインリッヒの法則とは、1件の重大事故の背後には重大事故に至らなかった29件の軽微な事故が隠れており、さらにその背後には300件の障害のない事故が隠れているという法則です。
「障害のない事故」は障害がなくても事故なので、災害には至っていないヒヤリハットとは必ずしもイコールではないかもしれません。しかし重大な事故の背後にはより軽微な事故が隠れているということは事実だと言え、それを前提に対策を進めるべきでしょう。やはりヒヤリハットを減らすことで、軽微・重大な事故のリスクを大きく下げることができると言えます。
ヒヤリハットの原因
ヒヤリハットの原因は事例ごとにさまざまですが、いくつかのグループに分けることができます。
まず、作業の手順が不適切というケースです。危険性の軽視などにより、確認が不十分だったり電源を入れっぱなしにしていたりすることが挙げられます。
次に設備面に問題があるケースです。点検不足、問題点の放置などが挙げられます。フレコンバッグのベルトが切れた事例を紹介しましたが、使用前に点検していれば危険性に気付けた可能性があります。また紹介できませんでしたが、電源ケーブルの絶縁被覆が破損していて感電した例もありました。それも破損を修理していれば避けられたはずの事故です。
ほかには、環境が原因になる場合があります。整理整頓の不徹底、死角や段差など問題点の放置などです。
最後に人的な原因です。疲労・寝不足・体調不良などによる集中力低下や焦りなどのメンタル面の問題、技術不足や経験不足などスキル面の問題、判断ミスなどが考えられます。
ヒヤリハット活動と危険予知トレーニング
ヒヤリハットを減らすための組織的な対処として、「ヒヤリハット活動」と「危険予知トレーニング(KYT)」があります。
「ヒヤリハット活動」は、厚生労働省によれば「ヒヤリハットを集め、事前の対策と危険の認識を深めることで、重大な事故を未然に防ぐ活動」「 作業者ひとりひとりが出来る、安全活動のひとつ」とされています。
「危険予知トレーニング(KYT)」は、危険要因とそれがもたらす結果について、グループで話し合って解決を目指すものです。基礎手法となる「4ラウンド法」は、以下の手順で行います。
1、潜む危険の発見
2、中でも重要な危険の共有
3、解決方法を出し合う
4、話し合いとチームとしての解決方法の合意
いずれも対策に効果的だと言えるでしょう。
ヒヤリハットの対策
次に、より具体的な対策方法について解説します。マニュアルの変更、あるいは遵守の徹底などに以下の対策を反映させるとよいでしょう。「ちょっとだけだから」はヒヤリハットや事故のもとです。いつでも決められた手順を守ることが大切です。
次の手法別に解説します。
・確認の徹底
・手段・手順の最適化
・設備・環境の設定や改善など
・体調管理の徹底や休憩の確保など
1つずつ見ていきましょう。
対策 | 確認の徹底
まず作業前や作業中の確認を徹底することが挙げられます。
フォークリフトや台車などで運搬している間や動き始める前には、人がいないかなど周囲の環境を確認します。また機械や設備・備品の状態も、作業前に点検することが大切です。毎日の点検が難しいものやそこまで頻繁に行う必要がないものは、点検を行う周期を明確にしましょう。
また人と人との間の確認もヒヤリハットの防止に役立ちます。複数人数で作業する場合にお互い声掛けをし合うこと、朝礼時の情報共有などが挙げられます。
そのほか出勤時の体調や睡眠時間などの確認も注意力低下のリスク発見に効果的です。
対策 | 手段・手順の最適化
さらに、手段や手順を最適化することはヒヤリハットの予防につながります。
わかりやすい例では、清掃など機械の中に手を入れざるを得ない状況では機械の電源を切ってから作業することが挙げられます。作業中の道具の定位置を決めることも同様です。このように、機器の使い方や作業の手順を事故のリスクの少ない形にすることが大切です。
以上をマニュアルに盛り込み、遵守を徹底します。
対策 | 設備・環境の設定や改善など
危険がある、あるいは事故の原因になりうるような設備や環境を改善したり設定し直したりすることも有効です。
環境の例では、段差をなくすことや作業場所の照度を上げることなどが考えられます。また設備とも関わりますが、見通しが悪いところにセンサーを設置して危険なときにアラートを出すのも有効です。近年はRFIDなどの技術も進んでいます。そのほか整理整頓など5Sの徹底も、すぐに始められる対策です。
設備についても、内容によっては安全装置の装備や機械の設定の修正で対応できるでしょう。また機械に限らず、手袋・保護メガネなど人の装備を最適化する方法もあります。ただし手袋は、巻き込まれなどかえって危険になる可能性があるのは実例で見た通りです。注意してください。
対策 | 体調管理の徹底や休憩の確保など
人的な要因については、体調管理の徹底や休憩時間の確保などが対処方法として挙げられます。より具体的には、以下のような方法が有効でしょう。
・出勤時の体調チェック・検温など
・休憩時間の確保
・夏場の水分・塩分の補給など
・長時間労働を避けるなどシフトの工夫
・睡眠・食事、場合により服薬など本人の健康管理
上記のような対策により、集中力の低下の予防とそれによるヒヤリハットの抑止が期待できます。
ヒヤリハットの報告の内容
ヒヤリハットの再発防止には実態を把握することが求められ、ヒヤリハット発生時の報告が必須となります。次に、ヒヤリハットの報告に盛り込むべき内容を解説します。以下の3点です。
・事実の整理
・原因の分析
・考えられる予防策
上記の内容を盛り込んで報告書をテンプレート化し、それに記入していけば漏れがないようにすることが望ましいと言えます。また再発防止のためにも、発生したら速やかに報告することが大切です。
では、1つずつ見ていきましょう。
報告 | 事実の整理
まず、事実を整理して報告する/させることが大切です。5W1H、すなわち「いつ・どこで・誰が(担当者・当事者)・何をしていて(作業内容)・どうなった(ヒヤリハットの内容)」を整理しましょう。そのほか、そのときどのように対応したか、その結果どうなったかについてもまとめます。
事実の記述・報告には、主観をできるだけ入れないように注意・工夫することが必要です。とくに、報告者は自分の責任にならないようにと客観的に報告しない可能性もあります。
そのほか、当事者の部署でしか通じないような専門的な用語も避けるようにしましょう。
報告 | 原因の分析
事実を整理したら、ヒヤリハットがなぜ発生したのかを分析します。すでに解説したように、原因には人的な要因・外部環境・複合的な理由などいろいろなパターンがあります。
分析は客観的に行うことが重要です。報告を受ける側も、報告中の分析が客観的かどうか見極める必要があります。上述のように、自分の責任逃れのために本質的な原因を回避する可能性もあるからです。
報告 | 考えられる予防策
最後に、分析で得られた原因を取り除く方法・未然に防ぐ方法を検討します。必要なものであっても、作業をいくつも追加していくと現場の負担が大きくなって実行し続けることができなくなってしまいます。ときには作業全体の内容や量を最適化することも必要です。
また、考えうる最善の予防策に加えて、仮に起こってしまった場合の対応策も検討しておく必要があります。ヒヤリハットが発生しないよう対策することは大切ですが、万が一起こってしまったときにどう対応するかもまとめておくべきです。それがないと、いざというときに対処できないことになってしまいます。
報告をネタ切れと言わせない方法
最後に、報告をネタ切れと言わせないための方法についてまとめます。予防のためにこまめな報告をさせようとしても、徐々に「書くことがない」と言われるようになりがちです。以下の3つは、その対処方法です。
・報告内容の共有
・報告を評価・報奨金の対象に
・報告の習慣化
1つずつ見ていきます。
方法 | 報告内容の共有
まず、受けた報告結果は関係部署や管理者の間だけでなく全体で共有しましょう。報告が周知されることで、皆が報告の必要性や重要性を認識できるようになります。自分の報告が意味を持つという自覚を持たせることも可能です。
もちろん再発防止の観点からも全体で共有することは重要です。
方法 | 報告を評価・報奨金の対象に
報告を評価・報奨金の対象にするという方法もあります。その場合の大前提として、まずヒヤリハットを本人の責任にせず、報告者の評価・査定を下げないことが大切です。
報奨金などは、むしろ反対に改善のきっかけとして報告をプラスに評価するという方法です。インセンティブの例としては、「1回〇円」と一律で払う形や、「有益な報告に〇円」などという形があります。
インセンティブや評価の対象とすることで、積極的な報告の後押しになります。
方法 | 報告の習慣化
3つめの方法は、業務の1つとして定期的に振り返りと報告の時間を取る方法です。業務なので業務時間内に行います。
この方法を続けると、新しいヒヤリハットがないという意見が出るようになるかもしれません。その場合、過去の報告が生かされているかを検証させます。それにより過去の事例でも、新たな対策方法や改善した対策方法の検討に役立ちます。過去の確認は振り返りの機会としても有益です。
安全性・生産性の高い工場ならファクトリアにご相談を
工場でのヒヤリハット対策は、事故を減らす手立てとして有効です。効果を高めるためには、事前の対策のほか、新たな事例をもとに対策をブラッシュアップしていくことが求められます。
また、作業環境のヒヤリハットをゼロに近づけるためには、レイアウトや設備の根本的な問題を解決する必要があります。そのためには建設時のレイアウトや設備選びが重要です。
安全性・生産性の高い工場建設なら、私どもファクトリアにご相談ください。工場建設のトータルサービスブランドとして、設備や動線計画といったハード面だけではなく社員のモチベーション向上まで考えた提案をさせていただきます。このページの最上部、最下部からお問い合わせいただけます。お気軽にご連絡ください。
-
工場運営【倉庫や工場の防虫対策まとめ】発生源から考える防虫対策やリスク回避術
倉庫や工場では、リスク管理のひとつとして「防虫対策」は必須となります。中でも食品工場や製品を保管す…
-
工場運営工場の整理整頓の重要性|5Sの目的やメリットと取り組み方のコツ
工場の安全性・生産性向上の鍵となるのが「整理整頓」。そこで注目されているのが、単なる清掃や片付けで…
-
工場運営工場でのヒヤリハット事例まとめ【原因・対策・報告も解説】
工場で働いていると一度や二度は「ヒヤリハット」の経験があるのではないでしょうか。ヒヤリハットを放置…
-
工場運営工場における安全対策の基本|事故リスクゼロへ!安全のための取り組み方
さまざまな機械や資材があり、いつ事故が起きてもおかしくない環境下にある工場では、 「安全対策」が…