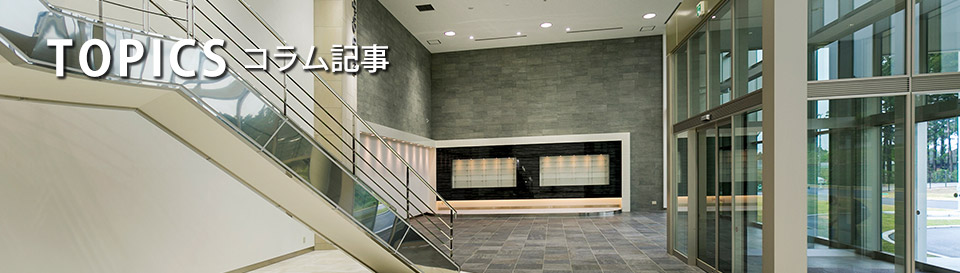
工場における安全対策の基本|事故リスクゼロへ!安全のための取り組み方
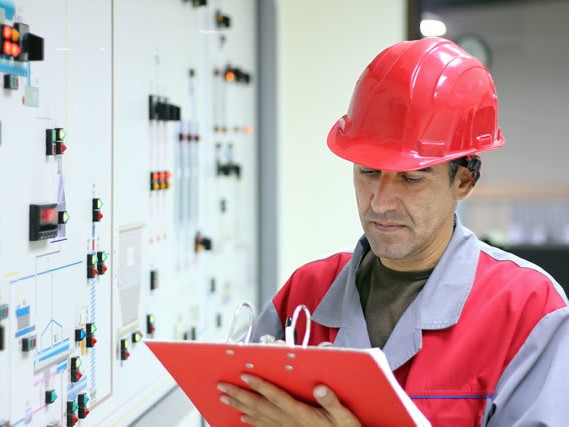
さまざまな機械や資材があり、いつ事故が起きてもおかしくない環境下にある工場では、
「安全対策」が欠かせません。
一歩間違えると重大事故につながる工場も多い中、労働災害ゼロを目指すことは用意なことではありません。事故が発生してしまうと、大事な従業員の怪我や事故につながり、さらに生産計画や企業の信頼にも影響します。
そこで重要になるのが、事故を未然に防ぐための安全対策です。本記事では、工場における安全対策の基本や取り組み方について解説していきます。
工場における安全対策の目的や重要性
工場では、機械の稼動やフォークリフトなどの移動、化学反応など危険要素が数多く存在しています。常に危険と隣り合わせで、僅かな不注意が大きな事故につながりかねない状況です。安全対策が不十分だと、怪我はおろか死亡者が出ることも少なくありません。
そうなれば、1つの事故をきっかけに企業は貴重な人材を失うばかりか、損害賠償や刑事罰を科される、社会的信用が低下し経営難に追い込まれる、ということも大いにあり得えます。
では、実際に工場で重視される「安全対策」の目的を次の項で見てみましょう。
工場内での事故を防いで従業員の安全を守るため
工場で安全対策を徹底する目的は、「労働災害を未然に防ぎ、怪我人や死亡者を出さないため」、つまり「従業員の命・安全を守るため」です。
工場内でのあらゆる事故を未然に防ぐことは、労働者一人ひとりの生命と健康を守る基礎であり、そのための安全対策は企業の最優先事項です。
どのような危険があるのかをしっかり把握し、安全のためのルールを全従業員で徹底し、守ることが求められます。安全対策を講じることで労働災害の発生を防止し、従業員が安心して作業を行える環境を整えることは工場運営において非常に重要なことなのです。
労働災害の発生要因は多数ある(ハインリッヒの法則)
労働災害の要因はヒューマンエラーに加え、機械・設備の不備や環境的要素など多岐にわたります。
実際、労働災害を防ぐための考え方として有名な「ハインリッヒの法則」では、「1件の重大な事故には、29件の軽い事故と300件のヒヤリハットがある」という理論が述べられています。つまり、大きな災害の背後には数多くの小さなエラーやミスが存在するという考えです。
この法則を元に考えると、重大事故を防ぐためには、小さなミスや災害を繰り返し起こさせないこと・ヒヤリハットの段階で対処することが重要だと言えます。
工場で起こり得る事故の種類
工場では様々な労働災害や事故が発生する可能性があります。それらを防ぎ、従業員の安全と健康を守るためにも、まずは工場で起きる事故について頭に入れておきましょう。
・挟まれ・巻き込まれ
・転倒
・転落・墜落
・切れ・擦れ
・感電・火災
・熱中症
挟まれ・巻き込まれ
工場では機械を使用して作業を行う場合が多く、挟まれや巻き込まれのリスクが常に存在します。機械の取り扱いをひとつ間違えれば重大事故になり人命を失うことも…。
挟まれや巻き込まれの原因は、機器の部品が飛び出してくるなどの「機器の整備不良」や、従業員が機械に手や体を近づける・操作を誤るなどの「ヒューマンエラー」が主ですが、原因に関わらず、重傷を負う事故が多い現状です。
転倒
転倒事故は工場内で最も発生しやすい事故の一つですが、場合によっては体を強く打ち、大怪我につながる恐れがあります。何かを運搬中にバランスを崩して転倒したり、作業中に床の突起物につまずいて転倒したりするなど、機械や物が多くある工場では特に起こりやすい事故です。
本人の不注意や作業環境の問題が原因となることが多く、床面の滑りや不適切な靴の使用、床面の障害物などささいなことが事故につながります。また、転倒した先に危険物があったり、フォークリフトなどが走行していれば、重大な怪我を負ったり、最悪の場合死亡に至るケースもあります。
転落・墜落
高所作業による転落・墜落事故や段差や階段からの踏み外しなどは、きわめて重大な事故をもたらすことが多いです。足場や安全柵の不備、足場の不安定さや強度不足、段差の存在、従業員の不注意などが原因で起こります。
工場では、はしごや脚立、フォークリフト、クレーンを使った高所作業の際に転落する墜落・転落事故の労働災害も多い傾向にあります。
切れ・擦れ
切れ、擦れといった怪我は、工具の使用や資材の取り扱い中に多く起こります。また、工場に設置されている機械の中には刃物が装備されているものも多いため、切れの事故が多い現状です。
さらに、業務用カッターやスライサー、電動丸のこなどに誤って接触し、指を切ったり、切断したり、それにより出血多量で死亡するなどの労働災害も実際に報告されています。
感電・火災
感電は、作業中に電源コードに触れる、絶縁不良の機械の使用、不適切な配線、保護装置の欠陥、電気機器の故障、作業者の不注意や慢心など様々なことが原因で起こります。
感電事故によって重度の火傷や意識不明、心臓停止などの重傷を負うことがあり、場合によっては死亡するケースもあるので注意が必要です。
また、火災は電気機器の使用や溶接作業が原因となることが多い傾向にありますが、意外にも機械の修理や点検を行う際にも発生しやすいと言われています。
熱中症
近年、夏場には連日のように猛暑が続き、熱中症の症状を訴える方も多いです。工場(屋内)にいるから安心というわけではなく、工場内での作業にも熱中症のリスクが潜んでいます。
特に夏場や、高温多湿の環境下での作業においては熱中症のリスクが高まります。
工場の安全対策に導入するべき3つの取り組み
工場の安全対策は、労働災害を防止し、従業員の安全を保つために必要不可欠です。そこで、効果的な安全対策の取り組みとしてよく挙げられる以下の3つを、1つずつ順番にご紹介していきます。
・5S活動|整理・整頓・清掃・清潔・しつけ
・KYT|危険予知訓練
・ヒヤリハット活動
より取り組みの成果を高めるためのポイントについてもあわせてご紹介していきます。
5S活動|整理・整頓・清掃・清潔・しつけ
5S活動とは、工場の作業場所を効率的に管理し、安全性・生産性を改善するための活動基盤です。作業環境を整えることで、事故のリスクを減らす効果が期待できます。
ただし、5S活動は、その場限りではなく継続していくことが安全対策の観点からも非常に重要です。5Sを現場に定着させることで安全意識の向上を目指しましょう。5つのSを1つずつ解説していきます。
整理
5Sにおける整理の目的は、事故の原因を取り除くことにあります。具体的に整理とは、必要なものと不要なものを区別し、不要なものを処分することです。使わないものを放置しておくと衛生面や作業環境が悪化し、万が一の事故の際、放置していたものによって被害を拡大させる危険もあります。
つまり、工場における整理という作業は、不要なものを排除することで、作業の効率化と安全性を確保する重要なステップなのです。必要のない工具や材料を取り除くことで、余計な障害物が作業場所からなくなり、転倒や怪我のリスクを減少させます。
整頓
整頓とは、ものの定位置を特定し、それを明示する活動です。作業場がもので溢れ、散らかっていると危険要素に気付きにくくなります。
一方、工場内の「どこに、何があるのか」を一目で分かるようにすることで、緊急時の対応速度が上がり、事故や緊急時の安全確保につながります。また、工場安全標識表示の適切な配置も整頓の一環として効果的です。
清掃
清掃は汚れを取り除き、機械や設備をはじめとする作業環境を常にクリーンに保つ活動です。積極的な清掃活動は、油や液体による滑りや転倒を防ぎ、火災予防対策にもなるでしょう。
また、清掃は機械や設備のメンテナンスも含みます。これらを定期的に行うことで、機械の異常や初期の劣化などを早期に発見できることも多く、これによって機械の適切な保守管理が可能です。結果的に、大きな事故へと発展することを防ぐことができます。
清潔
清潔は、ここまで紹介した「整理」「整頓」「清掃」の3Sを維持することを指します。
清潔な労働環境を維持することは、従業員が気持ちよく仕事に臨むことができるだけでなく、安全対策上も極めて重要です。整理や整頓、清掃を通してはじめて清潔さが保たれ、事故が起こりにくい環境づくりが叶います。
しつけ
しつけは、ほかの4つのSを定着すること、つまり従業員全員が5Sを定着化することです。従業員が実践できるルール作りと、それを守る習慣を身に付けることが重要。
5S活動により全従業員の安全意識が高まり、ルールを徹底することが定着すれば、事故が起こりにくい環境が生まれるでしょう。
KYT|危険予知訓練
工場で事故を未然に防ぐためには、「KYT(危険予知訓練)」が重要な役割を果たします。
このKYTは、「危険(Kiken)・予知(Yochi)・トレーニング(Training)」の頭文字をとったもので「危険予知訓練」とも呼ばれ、労働災害の防止を目的に、危険に対する感受性や集中力、問題解決能力を高めるために行う訓練のことです。
このKYTの実施によって、従業員自らが危険を察知し、事前に防止できるようになるため、事故の発生率を抑えられることに期待できます。
なお、KYTには「基礎4ラウンド法」と呼ばれるトレーニング法があり、主に事故が発生しそうな状況のイラストを見ながら行うパターンと、実際の現場を見ながら行うパターンがあります。手順は次の項目で順番にご紹介していきます。
1R|潜んでいる危険を把握
安全対策の基本は危険の把握から始まります。1Rは、どんな危険が潜んでいるのか、事実をつかむ現状把握の段階です。KYT訓練用のイラストシートまたは、実際の職場や作業をもとに、工場に潜んでいる危険要因について複数名で話し合います。
危険要因によって実際にどんな危険・事故が起こるかを想定し、メンバーから出た意見をすべて挙げて書き出します。実際に事故が起きるかどうかではなく、危険だと思われることをすべて挙げていくのがポイントです。
2R|原因を探る
2Rでは、1Rで挙がった考えられる危険の中から、重要だと思われる項目に◯をつけていきます。この〇の中からさらに重要なものを絞り込み「◎:危険ポイント」とします。最も危険とする◎は、チーム内において満場一致で決定することが重要です。
たとえ意見が分かれても多数決にせず、話し合いによってメンバー全員が納得できるものを導き出すことが大切。そのうえで、特に重要と判断した◎を全員で指差しながら唱和しましょう。
なお、選定段階での話し合いは、従業員同士のコミュニケーションの活性化と、危険の本質(原因)を追究するためにも非常に重要です。
3R|対策を立てる
3Rでは、2Rで挙げられた「◎(危険ポイント)」を解決する「対策」について、意見を出し合い、そのすべてを書き出します。この段階では、一人ひとりが「自分ならどうする」といった視点で考えることが重要です。
また、「気をつける」「注意する」といった意識には個人によってもバラつきが生じるため、対策にはなりません。具体的かつ実践できる対策を立てることを心掛けましょう。
4R|行動計画(目標)を決める
最終段階の4Rでは、3Rで出た対策をもとにメンバーで話し合い、全員の合意を得て、行動計画を決定します。その後、実行するための行動目標を設定します。
例えば、「◯◯するときは△△を××して□□しよう!ヨシ!」と、全員で行動目標を唱和して確認し合いましょう。
もし全員が目標設定に賛同できない場合は、1~3Rで決めたことに不備がなかったか再度振り返り、話し合いを重ねたうえで全員が納得できる行動目標を立てることが大切です。
ヒヤリハット活動
「ヒヤリハット」とは、危ないことが起こったものの、幸い重大な事故には至らなかった事象を指します。本記事の初めの方でも触れましたが、重大な事故には、それに至るまでに「ヒヤリとしたりハッとしたり」するような小さな危険が積み重ねられているとされています。
そうした危険事例を集めて対策を立て、事故防止につなげることが、「ヒヤリハット活動」と呼ばれるものです。
ヒヤリハットを全従業員で共有し、改善策を検討して重大な事故の防止を目指すことが目的です。日々のヒヤリハットの共有によって、全従業員の安全意識を高め、重大事故を予防することが求められます。
工場に潜むヒヤリハットの洗い出し
工場内には見過ごされがちなヒヤリハットが多々存在します。従業員が日々の作業中に感じる違和感や危険信号を積極的に捉え、細部に渡って記録を行うことが重要です。
実際に体験している小さなミスも、未来に起こる可能性のある重大事故を防ぐヒントとなるので、見逃さないようにしましょう。また、具体的な危険要因を把握し、ヒヤリハットを従業員同士で共有することで、同じシチュエーションによる事故発生を防ぐことができます。
ヒヤリハットを洗い出す際は従業員に対して、定期的にどのようなヒヤリハットがあったかについてヒアリングを行うことが大切です。また、ヒアリングをしなくとも、日頃から「ヒヤリハットを収集できる仕組み」を作っておくことも重要です。
報連相の徹底・報告書の習慣化
報告・連絡・相談の徹底は、安全対策を推進する上で欠かせません。ヒヤリハットが生じた際には、迅速かつ正確な情報を上司や関連部署に報告する体制を整えるべきです。この報連相を徹底することで、事故を未然に防げる確率が高まります。
また、ヒヤリハットを報告する報告書は、事例ごとに丁寧に綴り、それを習慣化することで、従業員全員が安全情報を共有しやすくなるので非常に重要です。また、のちに対策立案の基盤にもなるため、詳細を記載した質の高いものが求められます。
ヒヤリハットの事例を記録し、報連相を実践することで「重大事故の防止=安全対策」につなげましょう。
対策の立案・マニュアル化
工場内で特定されたリスクに基づき、具体的な対策の立案とそのマニュアル化に取り組むことも大切です。機械や設備を扱う際には、曖昧な記憶を頼りにした操作では大変危険です。ヒヤリハットで終わればいいですが、最悪の場合、死亡者を出す可能性もあります。
そうした事態を避けるためにも、作業手順を記した手順書を作成し、新人~ベテランまで手順書に沿って正しく作業するよう指導しましょう。
また、マニュアルに落とし込み「見える化」することも大事!全従業員が実践できるような明確な指示を含むべきであり、この見える化・マニュアル化が安全対策の定着に役立ちます。
従業員のメンタルケア(従業員を責めない)
工場での事故は、従業員の不注意や集中力の低下によっても引き起こされます。そのため、労働環境の改善をはじめ、相談できる風土づくりなど、従業員のメンタルを良好に保つための対策が必要です。
また、何かしらのミスやヒヤリハットが発生した場合でも、報告しやすい環境作りのために、決してヒヤリハット事例を発生させたことを責めてはいけません。報告してくれた従業員に不利益がないようにするのも大事です。
さらに、ヒヤリハット報告書を提出したものの、その後工場内でどのように役立てられたのかが分からなければ、報告書を作成した従業員の意欲は削がれ、次のヒヤリハットの報告を怠ってしまうかもしれません。そのため、ヒヤリハットを集めるだけでなく、適切なフィードバックも大事です。
従業員に共有・意識アップ
従業員全員が安全意識を持ち続けることで、危険予知活動の質が向上します。実際のヒヤリハット事例を共有し、従業員が自ら考え行動できるように教育することが重要です。
5Sの徹底以外にも、工場内では走らない、床に物を置かない、使った工具はもとあった場所へ戻すなどのルールも定期的に従業員に示す必要があります。ルールを正しく認識して守ってもらうためには、繰り返し定期的に伝えることが必要です。
定期的な改善
工場の安全環境は常に変化するものです。そのため、安全対策を決めたからといって、一度で完璧なものができるわけではありません。対策を講じた後も、その効果を検証し、新たな問題が生じていないか定期的にチェックすることが肝心です。
また、落とし込むときに気づいたことや、実際に作業している人の意見も聞きながら、よりよいものにブラッシュアップしていくことが求められます。新しい設備の導入や作業内容の変更を行う場合も、安全対策を見直す必要あると言えるでしょう。
工場の安全対策には危険の「見える化」が重要
工場における安全対策では、潜在的な危険を可視化することが必須となります。工場内での危険箇所や事故が起こりやすい場所を視覚的に明確にしましょう。
この見える化により、従業員が危険に対して注意を払いやすくなるため、事故を未然に防ぐことができます。危険箇所に対して視認性の高い表示を施したり、監視カメラを用いて作業を外部から見えるようにしたりと、「見える化」の方法は多岐にわたります。
工場の安全対策ならファクトリアへご相談を
工場では、少しのミスが大きな事故に発展する危険があります。本記事を参考に安全対策の取り組みを進め、事故の発生を抑えて、全従業員が安全かつ安心して働ける環境を作りましょう。
なお、従業員の意識アップや取り組みの定着化も重要ですが、安全対策の根本を考えた時、工場そのものの見直しが必要な場合もあります。私ども【ファクトリア】は、工場の安全対策に豊富な実績を持つ、工場建築のトータルサービスブランドです。
お客様の工場の状況やご要望に合わせて、最適な安全対策をご提案させていただきますので、安全対策にお悩みの際はお気軽にご相談ください。
-
工場運営【倉庫や工場の防虫対策まとめ】発生源から考える防虫対策やリスク回避術
倉庫や工場では、リスク管理のひとつとして「防虫対策」は必須となります。中でも食品工場や製品を保管す…
-
工場運営工場の整理整頓の重要性|5Sの目的やメリットと取り組み方のコツ
工場の安全性・生産性向上の鍵となるのが「整理整頓」。そこで注目されているのが、単なる清掃や片付けで…
-
工場運営工場でのヒヤリハット事例まとめ【原因・対策・報告も解説】
工場で働いていると一度や二度は「ヒヤリハット」の経験があるのではないでしょうか。ヒヤリハットを放置…
-
工場運営工場における安全対策の基本|事故リスクゼロへ!安全のための取り組み方
さまざまな機械や資材があり、いつ事故が起きてもおかしくない環境下にある工場では、 「安全対策」が…