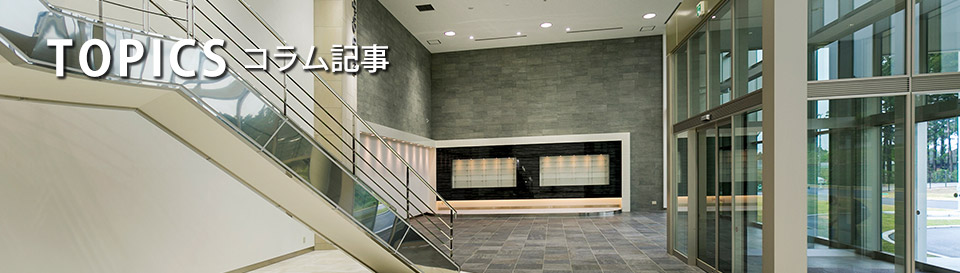
工場の整理整頓の重要性|5Sの目的やメリットと取り組み方のコツ
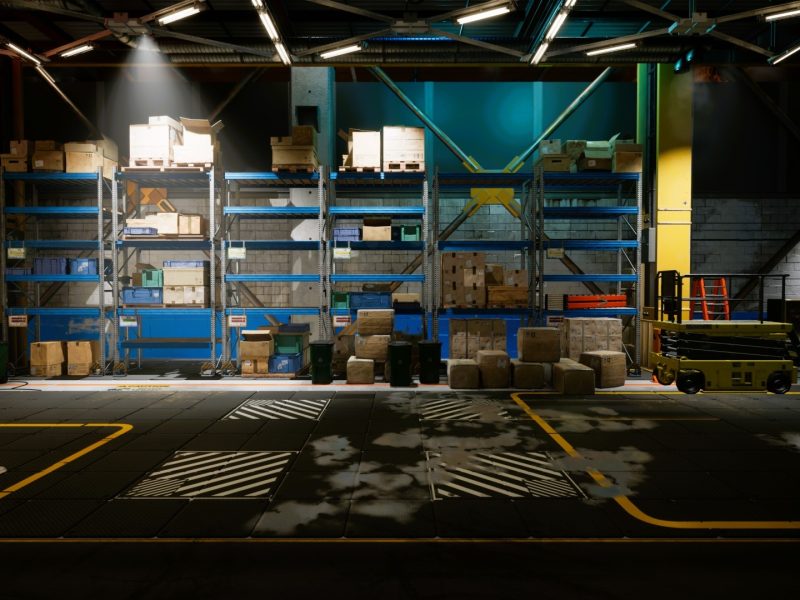
工場の安全性・生産性向上の鍵となるのが「整理整頓」。そこで注目されているのが、単なる清掃や片付けではない「5S」という手法です。工場の業務や環境の改善を進める手法として効果的な5Sの実践は、現在の工場運営においてもはや必須の要素となっています。
本記事では、5Sの基本的な概要や目的、5Sがもたらすメリットや取り組みのコツをご紹介します。続きを読むことで、5S導入によって「見える化」された効率的な職場へと変わるためのヒントを得られるでしょう。ぜひ最後までご覧ください。
工場における整理整頓の重要性
整理整頓は、工場の運営にとって極めて重要な要素です。作業環境を適切に保つことによりはじめて、生産性と安全性を両立させることができます。
多くの工場では、整理整頓を基礎として、労働環境の向上や生産性の向上策を日々追求しているはずです。そこでまずは、具体的に工場における整理整頓の重要性を頭に入れましょう。
安全管理のため
従業員が働き、多くの機械を扱う場所である工場にはさまざまな危険が潜んでいるため、適切な安全管理が求められます。
工場内での安全性を強化するためには、整理整頓が必要不可欠。というのも、床に不要なものが放置されていたり、通路にものが落ちていたりすると、従業員がつまずいて怪我をする、重機による事故が発生するなどのリスクが高まるからです。
裏を返せば、整理整頓が定着し、きれいな職場環境を維持することができれば、労働災害や事故を未然に防ぐことができるというわけです。整理整頓によって可視化管理が容易になり、危険箇所が明確になるため、効果的な安全対策が可能となります。
作業効率アップ
整理整頓は作業効率を高めるための基本です。整理整頓では不要なものを処分し、必要なものをきちんと管理することにより、作業効率アップを図ることができます。
たとえば、工場内で部品や道具、指示書などの必要なものがすぐに手に取れる環境では、作業工程が最適化され、非効率な動きが削減されます。
必要なものを探す手間も省けるうえ、時間のロスを発生させずスムーズな作業が叶うため、従業員はより作業に集中できるでしょう。それにより作業効率がアップし、同時に品質向上にも寄与します。
ヒューマンエラー防止
ヒューマンエラーをなくすことも、工場における整理整頓の目的のひとつであり重要なポイントです。整理整頓された作業環境は、工具や資材の保管場所が明確で、誤って間違ったアイテムを使用するリスクを減少させます。
つまり、整理整頓を徹底することにより、従業員が正しい工程を遂行しやすくなり、ヒューマンエラーを防ぐことができるのです。
工場の整理整頓で必要な「5S」とは
「5S」は工場などの作業場所を効率的に管理し、安全性と生産性の向上を目指すための活動基盤です。
この5S活動を通じて、従業員一人ひとりの意識を高め、整理整頓を習慣化することが求められます。ここからはより具体的に、大事な5つの「S」について解説していきます。
整理|不要なものを処分する
整頓|必要なものをすぐに取り出せる最適な場所に置く
清掃|きれいに掃除・メンテナンスをおこなう
清潔|清潔な状態を維持する
しつけ|4つのSを従業員全員が習慣づける
1つずつ詳しくみていきましょう。
整理|不要なものを処分する
整理とは、必要なものと不要なものを区別し、不要なものを処分することです。これにより作業スペースを効率化し、余裕を持たせることができます。
また、不要なものを極力削減することで、工場内の動線がスムーズになり非効率要因を省くことが可能になります。
ゴミを捨てたり、物を置き直したりするだけの、いわゆる「ただの掃除」だけでは一時的な効果しか表れません。つまり、その場しのぎではなく、継続して整理が行える仕組みを作っていくことが必要なのです。
整頓|必要なものをすぐに取り出せる最適な場所に置く
整頓とは、整理をしたあと、取り出しやすい最適な場所に必要なものを配置し、効率よく作業が行えるよう整えることです。工具や資材の管理方法を見直し、標準化オペレーションに基づいたシステム化が必要となります。
また、それらを従業員全員で共有することが大事です。口頭で伝えるだけではなく、一覧表を張り出しておいたり、看板を付けたりするとよいでしょう。たとえ置き場を覚えられない人でも、それを確認すれば誰でも「どこに、何があるか」を確認でき、スムーズに作業ができる状態にすることが肝要です。
さらに、置き場が未定のものを保管する仮置き場を設けると、通路を塞いだり、必要なものと混ざったりすることがないため、よりミスや事故を防ぐことにつながります。
清掃|きれいに掃除・メンテナンスをおこなう
清掃は、場所をきれいかつ清潔に保つ活動です。日頃の清掃を丁寧に行い、気持ちのよい環境作りをすることが求められます。機械や道具の点検・メンテナンスも清掃の一環です。
定期的に徹底した清掃を行うことで、設備の早期の不具合発見や故障防止、製品の品質維持に寄与します。清掃を徹底することにより、重大なミスや事故を防ぐことが可能です。
清潔|清潔な状態を維持する
清潔とは、清掃によって得たきれいで清潔な状態を持続させることを意味します。つまり、これまでの整理・整頓・清掃ができている状態を維持することです。
従業員が自発的に清潔を心がけることで、工場全体の環境改善が期待され、また生産現場としての信頼性を高める要因にもなります。
汚れてからきれいにするのではなく、常に作業しやすい環境になるように心がけることが清潔を保つうえで非常に重要です。
しつけ|4つのSを社員全員が習慣づける
しつけは、整理・整頓・清掃・清潔を習慣化し、文化として根付かせることです。従業員自身の労働環境改善に対する意識向上のために、4つのSを日常的に実践し、持続可能な改善活動を展開していくことが目指されます。
なお、4つのSは一度実施しただけでは意味がありません。実行するための共通ルールを定め、従業員全員が習慣化できるようにすることが何より大切。新入社員の入社時や部署移動でも、全員が確実に実行できるレベルでのしつけが重要です。
5S活動の目的やメリット
5S活動は、整理・整頓・清掃・清潔・しつけの5つの「S」を基本に、職場環境の改善を図るものです。
この取り組みは、工場をはじめとする様々な現場で、品質や効率の向上に資すると同時に、安全性向上や社員の意識改革にも大きな影響を及ぼします。ここからは、具体的に5Sの目的やメリットをご紹介していきます。
・安全性の向上
・作業効率アップ・生産性の向上
・QCD(品質・コスト・納期)の改善・向上
・職場環境の質向上
・企業イメージアップ
・保全業務との連携
・従業員の連携強化・モラルマネジメント・モチベーションの維持
1つずつみていきましょう。
安全性の向上
工具や資材が乱雑に置かれた工場では、作業中に思わぬ事故を招くリスクがあります。また、適切なメンテナンスが行われていない状態で工具や機械を使うと重大な事故の危険も高まるでしょう。
その点、5S活動により不要なものの処分や最適な定位置の設定が行われれば、障害物が減少することで、つまずきや落下物による怪我や事故を防ぐことができます。また、メンテナンス不足による重大事故のリスクも減らせます。
5Sの徹底は労働環境改善への第一歩であり、従業員の安全意識を高めることにも寄与します。つまり、5S活動には「工場を安全な環境に整え、労働災害を防ぐ」という重要な目的があるのです。
作業効率アップ・生産性の向上
工具や資材などが乱雑に置かれている状態では、作業に必要なものを探すという無駄な時間がかかってしまいます。一方、5S活動を通して整理整頓が徹底できれば、業務に必要なものや情報を短時間で見つけることができ、時間の無駄や非効率な動作が削減されます。
こうして作業工程の最適化を図ることができれば、結果として作業の実行速度が上がり(作業効率アップ)、生産性向上策としても有効に機能することが期待できるでしょう。
QCD(品質・コスト・納期)の改善・向上
5Sは作業環境を整えるだけではなく、QCD(Quality品質・Costコスト・Delivery納期)の改善にもつながります。
作業環境を整えることで、従業員の集中力や判断力などが向上。集中して無駄のない作業が叶うため、納期に余裕を持てるうえ、品質の向上も見込めるようになるのです。
また、不要なものが整理されているので、工具や資材を探す、あるいは見つからないことで追加発注してしまうといったコストの削減も可能になるでしょう。1つ前でご紹介した作業効率アップにより、コスト削減だけではなく、納期の短縮にも効果的と言えるのです。
職場環境の質向上
整理整頓や清掃などの5Sが徹底できず清潔さに欠ける工場は、社内ルールやモラルの軽視、集中力の低下、モチベーションの低下、事故の発生といったマイナス面が多く見られるのが現状です。
一方、5S活動によって整えられた職場は、清潔で快適な環境を提供。より良い環境が保たれることで従業員のストレスが軽減し、きれいな職場で働けることによる従業員の満足度も高まります。
また、5S活動におけるルール決めや話し合いを通じて、従業員同士のコミュニケーションも増やせることから、結果的に工場の全体的な「質」を高めることにも期待できるでしょう。
企業イメージアップ
5Sを導入することで企業イメージをよくすることができるのもメリットの一つです。5Sが実施され、常にきれいな状態の工場は第一印象が良くなり、取引先や就活生、中途採用者に安心感や信頼感を与えることができるでしょう。
また、清潔さは、工場の安全性が確保されており、質の高い製品を作ることができるという証でもあるのです。こうしたイメージアップが、取引先や顧客からの信頼を得て、新たなビジネスチャンスの創出に貢献することもあります。
さらに、社内外に対して誇れる職場環境を作ることによって、従業員の帰属意識も刺激できるでしょう。
保全業務との連携
5S活動の実践は、保全業務と密接に関わり、良い影響をもたらすことも知られています。整理・整頓・清潔を保持していくためには、機械や設備のこまめなメンテナンス・清掃を行う必要があります。
機械や設備のメンテナンスや清掃をルール化・ルーティン化すれば、設備や機械の異常を早期に発見でき、予期せぬ故障やトラブルの事前防止につながります。結果的に、安定した生産活動を支える(生産ロスを防げる)ことができるでしょう。
従業員の連携強化・モラルマネジメント・モチベーションの維持
工場内の環境が乱れていると無駄が発生しやすく、事故の発生リスクも高まります。一方、5S活動が徹底されたきれいな職場は無駄な作業が減り、気持ちよく働けることで従業員のモチベーションがアップするでしょう。
また、5S活動は従業員が協力して行い、連携力を強化する機会を創出します。工場の整理整頓やメンテナンスなどの活動に取り組むことで、従業員一人ひとりの作業環境への意識を高めることも可能です。
5Sをルールとして守るという風土が向上全体で生まれれば、主体的に作業環境が整うようになります。また、組織全体で取り組むことでモラルが向上し、労働環境の向上といった、ポジティブな効果が相互に生まれるでしょう。
5S活動のポイント
おさらいになりますが、5S活動は5つの「S」により、工場の安全性や作業効率の向上を図る手法です。ここからは5S活動のポイントを具体的に紹介していきます。
・整理整頓の計画・目標を立てる
・不要なものを洗い出す
・「見える化」をおこなう
・5S活動の時間を確保する
整理整頓の計画・目標を立てる
整理整頓の計画を立てる際は、まず現場の把握から始めます。工場の業務フローを分析して、無駄な動きや時間が発生していないかを洗い出したうえで対策・目標を立てます。
なお、目標は具体的かつ達成可能なものでなければなりません。整理整頓を「いつ」「どの場所を」「誰が」「どんなものを」「どうするのか」と計画を立てることが大切です。最適化された作業工程を目指し、整理整頓マニュアルを基にしたチェックリスト作成が効果を上げるポイントでもあります。
また、5S活動は「1回で終わり」ではありません。話し合いを重ね、実施後も気付いたことなどをフィードバックし合い、より最適な整理整頓の計画を立てることが何より重要です。
不要なものを洗い出す
5S活動における整理作業では、使用しない工具、不要な在庫、余剰な設備などを徹底的に削減することが求められます。そのためにはまず、現場にどんなものが必要で、何が要らないのかを見極めることが大切です。
整理整頓を始める前に不要なものをまとめて処分したり整頓したりしてしまうと、後で「やっぱり必要だった」という状況になってしまう恐れもあります。そうならないよう、実行するときは、必ず「整理から」始めるのが基本です。
また、複数人で行うことにより、多様な価値観で判断でき、ほかの人・作業空間とも相対的に見比べることができるでしょう。
「見える化」をおこなう
「見える化」は、工場内の情報を分かりやすく表示することにより、誰もが状況を把握しやすくする方法です。整理整頓を成功させるポイントはまさに「見える化」の意識にあります。
たとえば、整頓の際には、置き場所を決めると同時に、自分以外の人でも正しく同じように整頓ができるよう「見える化」することが大事です。
また、どの場所に何があるかが分かるマニュアルを作れば、誰でも置き場所がひと目で分かり、探す手間もなくなります。見える化こそが作業効率を上げ、ミスを最小限に抑えることができる大事なポイントなのです。
5S活動の時間を確保する
5S活動は継続が重要です。そのため、5S活動のための時間を確保すること、つまり、従業員が定期的に整理整頓を行えるような工夫をすることが求められます。
たとえば、毎日5Sの活動時間を数分確保するだけでも大きな違いがあります。自分の作業範囲を整理整頓するだけでも快適な職場環境が整うように、毎日続けることはとても大きな効果をもたらすでしょう。
整理整頓された工場を維持・定着させるには
工場の安全な労働環境を実現させるとともに、生産性を向上させるために整理整頓は必要不可欠です。
そこで最後に、整理整頓された工場を維持・定着させるためのポイントをご紹介していきます。
・責任者を決める
・全社員で取り組む・意識改善
・定期的にチェックする
・5S活動の実施日を社内のスケジュールに組み込む
・工場の整理整頓を改善するアイデア
1つずつみていきましょう。
責任者を決める
整理整頓が持続する環境を実現するためには、まず特定の責任者を決めることが必須です。理想は、清掃や整頓の監督を行うチームや個人を指名し、それらの活動を調整する役割を担ってもらいます。
責任者は5S活動の推進者として機能し、メンテナンスを定期的に行い、労働環境改善にも取り組む必要があります。整理整頓マニュアルを作成し、他の従業員にその知識を伝えることも重要な役割です。5S活動の目的や方針、ルールを従業員全員に共有できる基本的な体制づくりを進めましょう。
全社員で取り組む・意識改善
5Sは、従業員全員で取り組まないと意味がありません。整理整頓の継続は、全従業員の共同作業と意識の変革にかかっていると言えます。
責任者が5Sのそれぞれの項目で何をすべきかを明確にし、共有します。誰もが無理なくできる内容にすることで、5S実施のハードルを下げることができ取り組みやすくなります。
これにより、それぞれの従業員が作業標準を守り、自分の担当エリアの在庫や工具を適切に管理することで、整理整頓が自然と行われるように促せるでしょう。
こうした工場全体の5S活動を通じて、整理や清掃の重要性について意識を新たにし、業務フロー改善や非効率要因の分析を行うことで、整理整頓の効果を最大化することが可能です。
また、現場の従業員だけではなく経営者が率先して実施する姿勢を見せることも、5Sの定着には欠かせません。
定期的にチェックする
整理整頓は一度行ったら完了というものではありません。定期的なチェックが必要であり、そのためには明確なチェックリストの作成が効果的です。
リストには、具体的な清掃ポイント、工具や資材の適切な配置、設備の状態などが盛り込まれ、継続的に5S活動が行われているかを評価します。
習慣化はいいことですが、場合によっては「なぜやっているのか」が不明瞭になり、いつしか「やらなくてもよいのでは?」といった気持ちが芽生えてしまうことも…。そうならないよう、それぞれの項目で効果の検証・改善を繰り返すことが大事です。
5S活動の実施日を社内のスケジュールに組み込む
5S活動は整理整頓のための強力なツールであり、この活動を社内のスケジュールに組み込むことも5Sの定着に有効な策と言えます。
整理整頓が日常業務の一部となるようにし、活動の実施日には、従業員全員が整理整頓に必要な労働環境改善や清掃に取り組みます。これにより、不要なものの削減やスペースの効率化など、効果的な行動・結果が見られ、日常的に「きれいが当たり前」の工場を保つことができます。
また、従業員間での整理整頓の取り組みを可視化管理することで、互いに良い影響を与え合い、改善活動に参加する文化や作業環境を整える意識を自然と生み出すことができるでしょう。
工場の整理整頓を改善するアイデア
あまり知られてはいませんが、工場の5S活動を促進する究極のアイデアとして「工場のレイアウトの見直し」も非常に有効な手段です。
大がかりな作業を要することも多いため、なかなか選択肢として挙がることはないものの、例えば工場の移転や改築、工場の新設などの機会があれば、レイアウトの見直しも検討してみましょう。
5S活動を意識した上でのレイアウト設計にすることで、より効果的な整理整頓の効果が見込めます。
整理整頓が定着しやすい工場建築ならファクトリアへご相談を
私ども【ファクトリア】は、快適な作業環境を実現し、企業価値を高める工場を目指す「工場建設のトータルサービスブランド」です。
整理整頓が定着した工場を実現するためには、工場建築の段階から、整理整頓を意識した設計・施工が重要となります。その点、ファクトリアは、整理整頓が定着しやすい工場づくりのお手伝いが可能です。
整理整頓にお悩みの場合や、工場のレイアウトの見直しを検討されている方は、ぜひ一度ファクトリアへご相談ください。
-
工場運営【倉庫や工場の防虫対策まとめ】発生源から考える防虫対策やリスク回避術
倉庫や工場では、リスク管理のひとつとして「防虫対策」は必須となります。中でも食品工場や製品を保管す…
-
工場運営工場の整理整頓の重要性|5Sの目的やメリットと取り組み方のコツ
工場の安全性・生産性向上の鍵となるのが「整理整頓」。そこで注目されているのが、単なる清掃や片付けで…
-
工場運営工場でのヒヤリハット事例まとめ【原因・対策・報告も解説】
工場で働いていると一度や二度は「ヒヤリハット」の経験があるのではないでしょうか。ヒヤリハットを放置…
-
工場運営工場における安全対策の基本|事故リスクゼロへ!安全のための取り組み方
さまざまな機械や資材があり、いつ事故が起きてもおかしくない環境下にある工場では、 「安全対策」が…